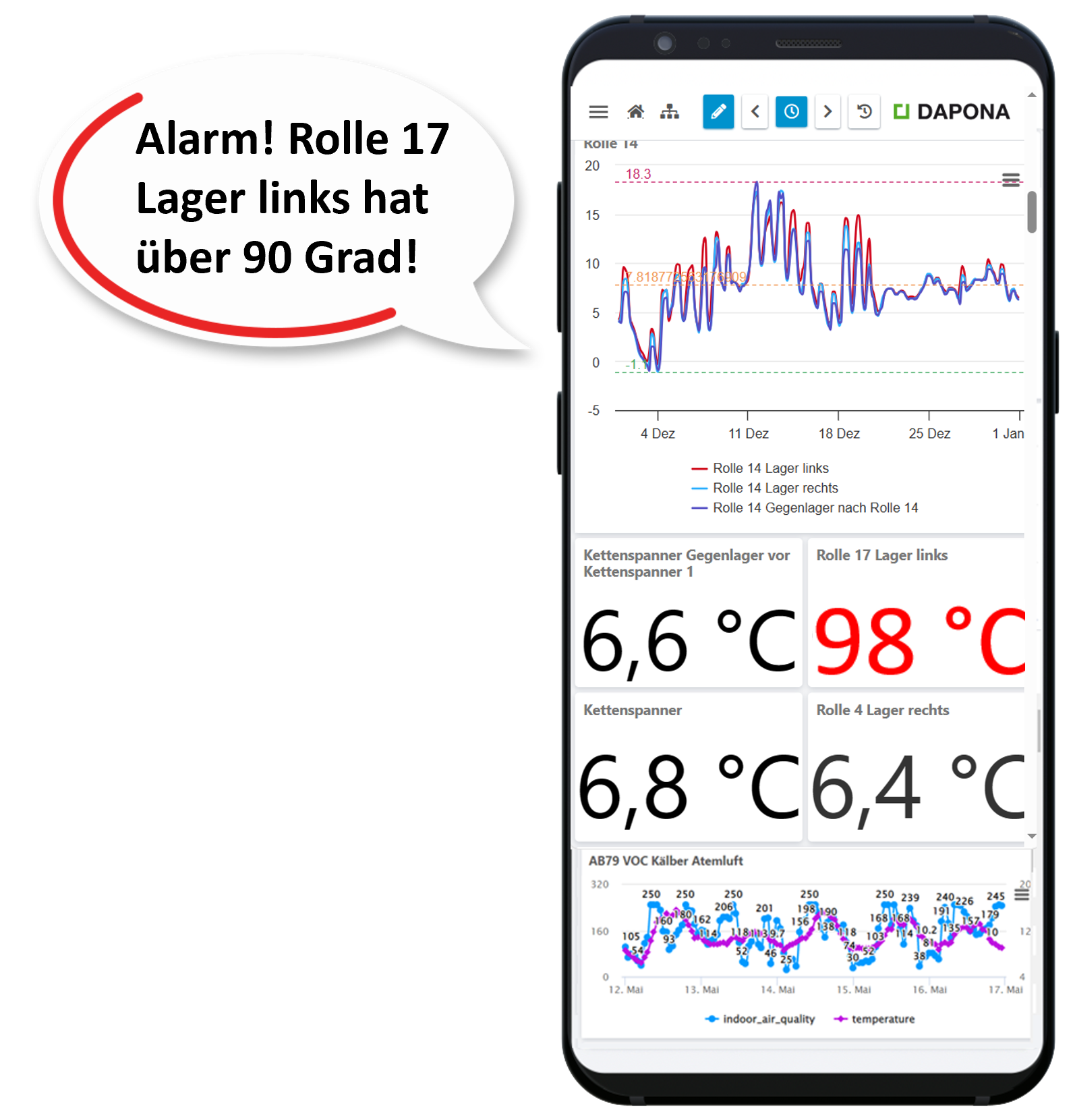
“Time and again we had pockets of embers in old warehouses. Now I can finally be sure that there will be no more fires. And I no longer have to check each bearing individually – a significant cost reduction, especially in this day and age…”
Maintenance manager at a sawmill
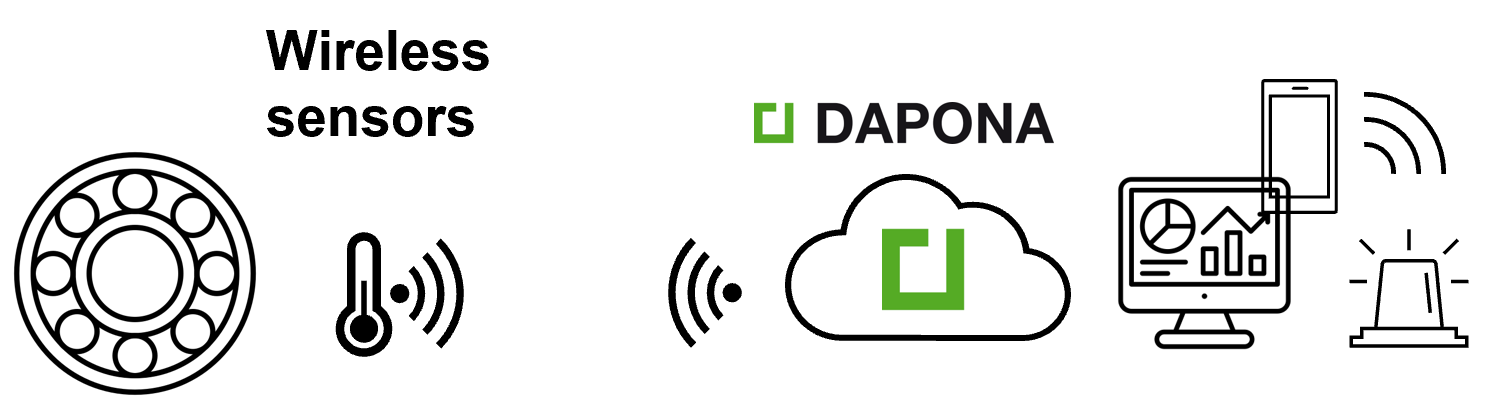
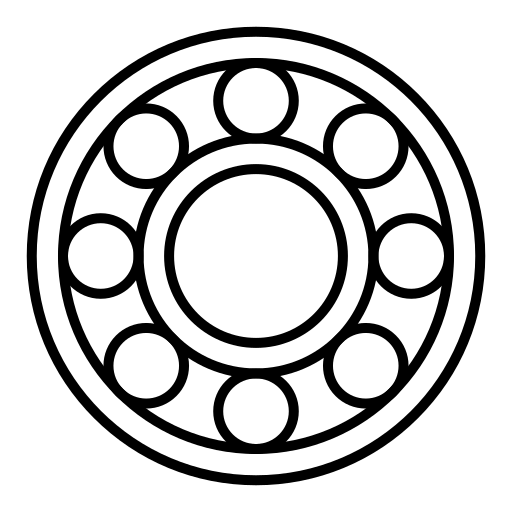
Risk reduction and avoidance of machine failures through timely alerting.
Ball bearings can heat up at some point. The problem: this often happens unnoticed. Production downtime, expensive repair costs due to blocked shaft bearings or even a fire can be the result.
With the multi-sensor wireless sensors from DAPONA, several shaft bearings can be easily equipped. As soon as a bearing starts to run hot, DAPONA sounds the alarm even before any damage has occurred.
Avoiding damage
to the motor and system
DAPONA helps to reduce the risk of damage. A sensor sends the warehouse temperature to the DAPONA digital platform around the clock. DAPONA records the progressions in real time and issues an alarm in the event of deviations. If the temperature exceeds a freely adjustable threshold value, DAPONA triggers an alarm. Multi-level alarms can also trigger signal lights or other actions according to freely definable rules.
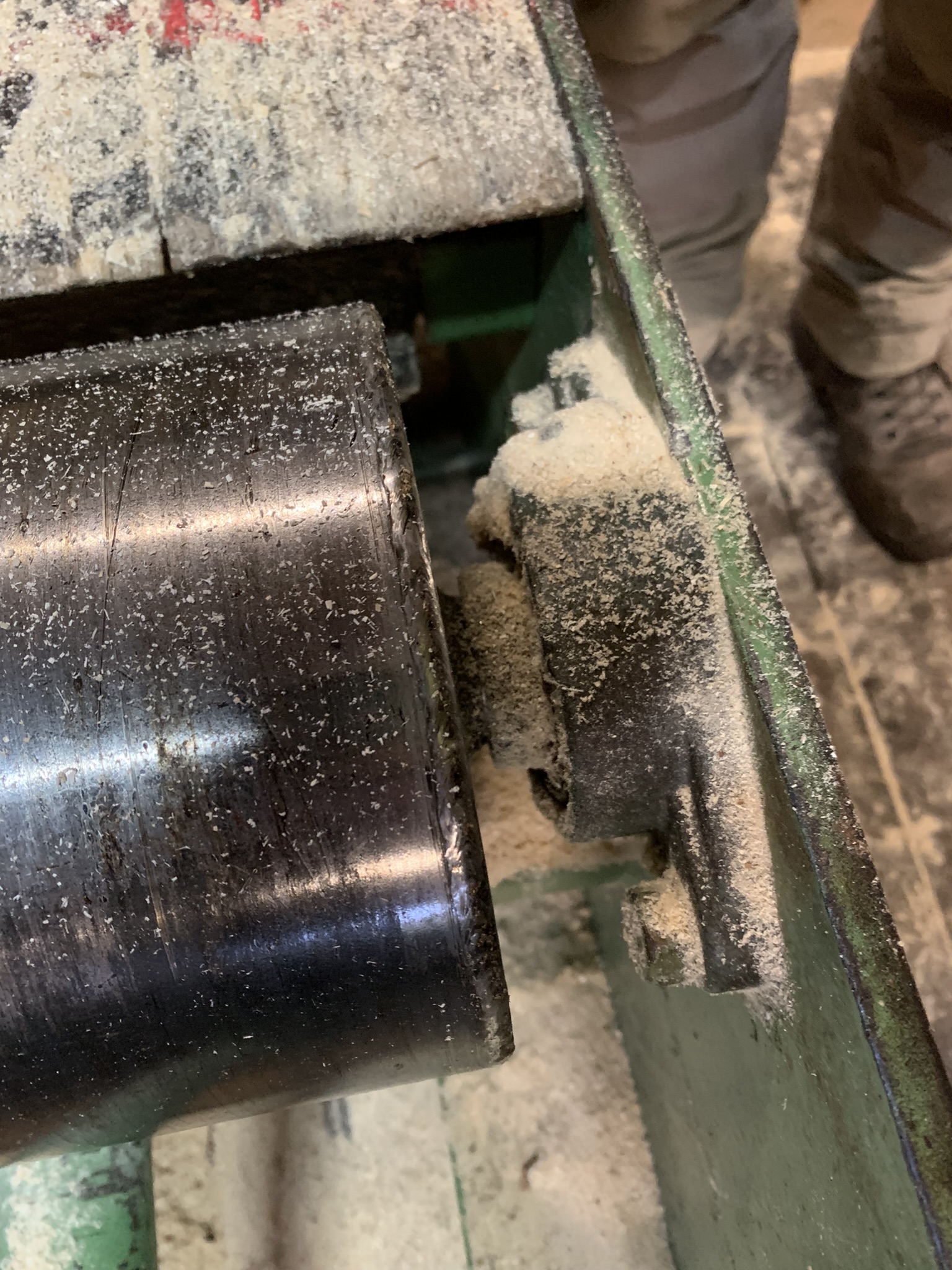
Fire risk reduced, production losses avoided
In a roller conveyor with over 30 rollers, glowing embers have repeatedly arisen due to hot bearings. An acute fire hazard that was constantly present as soon as the roller conveyor was in operation.
Each roller is fitted with ball bearings on both the left and right-hand sides. In addition, there are counter bearings on the drive side to deflect the drive chain between the rollers. The same applies to the motor and gearbox. The bearings are not only exposed to heavy loads from the rollers, which pull the cut boards out of the saw frame. It also happened again and again that sawdust nests formed during operation, which led to increased friction and overheating of the bearings. Despite regular cleaning, dangerous pockets of embers kept forming. It was very fortunate that the fires were always discovered in time.
Retrofitting the shaft bearings with multi-sensor wireless sensors. No system or radio control center required
This situation should now be put to an end. Each shaft bearing and the drive motor, including the gearbox, were fitted with a temperature sensor. Over 100 measuring points were recorded in this way.
The sensors send measured values to the IoT platform DAPONA 24 hours a day. The data is stored there and provides real-time information in freely configurable dashboards about
Condition of the shaft bearings (temperature index) Temperature of the drive motor and gearbox
DAPONA triggers a maintenance job in good time before a shaft bearing reaches the end of its service life, enabling the shaft bearings to be replaced in good time without causing any damage by aligning them with actual requirements.